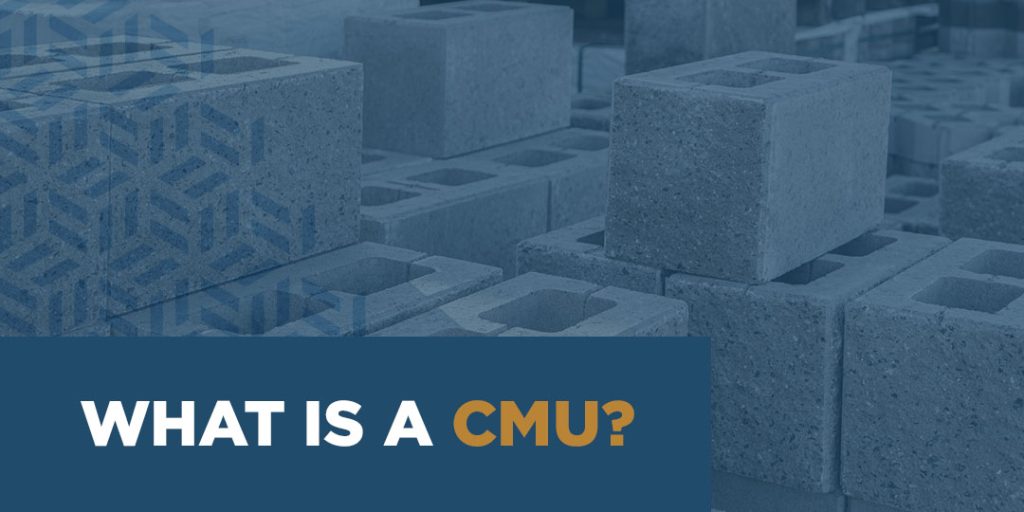
“CMU” stands for concrete masonry unit — a standardized, precast rectangular block used in several construction applications. Construction in any form requires reliable, durable and cost-effective materials. In addition to fulfilling these requirements, CMUs are easy to install and provide a flexible option for design and construction. In many ways, they offer the perfect material.
Masonry structures are the most commonly used materials in buildings and many other structures. As more end users require eco-friendly materials, knowing what a CMU is and what the benefits are is essential to meet customer needs and stay ahead of the competition.
What Is a CMU in Construction?
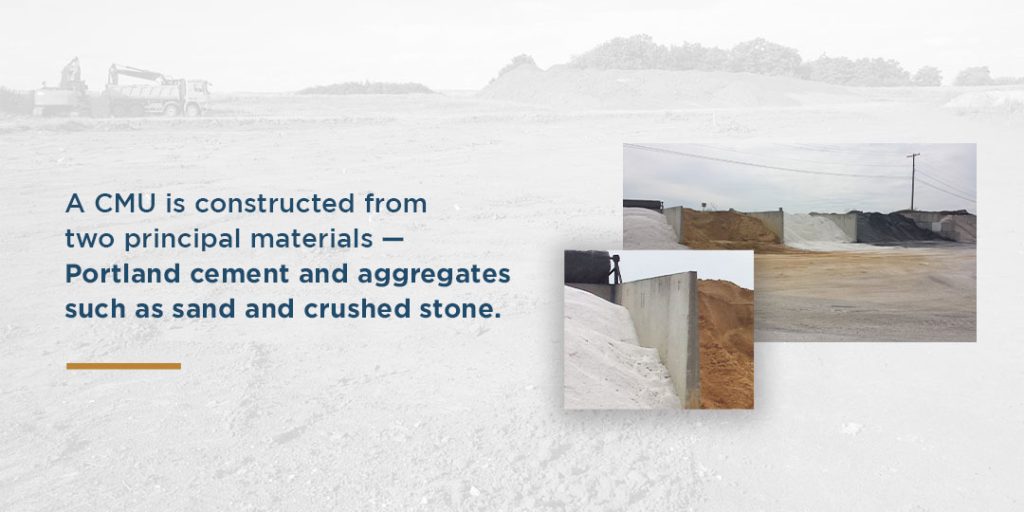
A CMU is constructed from two principal materials — Portland cement and aggregates such as sand and crushed stone. The aggregates form the block’s main structure, while the cement binds the aggregates together. Depending on the type of CMU and the intended application, the block may also include pigment to increase visual appeal.
The CMU manufacturing process includes:
- Mixing: The materials are measured into correct amounts and put onto a conveyor belt, which carries it to a mixer. The aggregates and concrete are combined with controlled parts of water to ensure the ideal consistency.
- Molding: When the mixture is combined correctly, it’s transported via a conveyor belt to a block machine and poured into the relevant molds. Compression is essential in this part of the process to ensure each block’s correct strength and height.
- Curing: Blocks are heated in a low-pressure steam kiln, where steam and heat are gradually introduced into the curing environment. Once the top temperature is reached, the kiln is shut down, and blocks remain in the warm, moist environment for 12-18 hours. Then, the humid air is drawn out, and the temperature is raised to dry the block.
- Cubing: Depending on the project, the appropriate finish is applied to the blocks, which are stacked on a wooden pallet and wrapped in plastic for easy transportation.
Once manufactured, CMUs are suitable for many architecture, construction and landscaping applications. A CMU wall is a common application for concrete blocks, secured with mortar for strength and longevity. When correctly manufactured and maintained, they can last up to 100 years, as the materials withstand deterioration over time, which means building with CMUs helps ensure the longevity and integrity of your structure.
The Benefits of Using Concrete Masonry Units
Choosing construction materials can take time, as you want to ensure you have the best possible end product. CMUs are one of several materials you can use, depending on the scope of your project and several other factors. The advantages of CMUs in construction include:
Energy Efficiency
CMU walls keep structures cooler in the summer and warmer in the winter, reducing heating and cooling costs and the associated environmental impact.
Sustainability
Manufacturing building materials often results in waste. However, concrete block is produced for each project, resulting in minimal wastage. Moreover, their energy-efficient properties reduce heating and cooling costs, which is better for the environment.
Concrete used in masonry applications like manufacturing CMUs can be crushed and reused as raw materials, making them recyclable. CMUs offer a sustainable and eco-friendly option from the manufacturing phase through their entire life cycle.
Low Maintenance
Concrete blocks require no staining, replacement or updating over their useful life, resulting in fewer maintenance costs and a user-friendly end product. They’re termite-resistant and don’t rust or rot with exposure to the elements, making them suitable for long-term outdoor applications.
Fire Safety
The CMU components — aggregates, water and Portland cement — are non-combustible, and concrete has low thermal conductivity, so it doesn’t transfer heat. In addition, it’s non-toxic and doesn’t react with other substances, so if there are gases or toxins involved in a fire, it won’t ignite. These qualities make CMUs a safe construction option to protect people and belongings. However, exposure to extreme temperatures for a long time can impact structural integrity.
Visual Appeal
CMUs can be manufactured to suit multiple designs, providing a contemporary styling option in many types.
Variety
You can choose from various block sizes to fit your design needs and applications. You can also make your project unique with different finishes and colors to suit your overall aesthetic.
Acoustics
Walls and other structures made from CMUs create an effective sound barrier, blocking out unwanted noise and creating a quieter environment, especially in busy housing areas.
Mold and Moisture
CMUs are more effective for waterproofing than poured concrete. Mold can only grow in moist areas, so easy waterproofing is essential to keep structures safe and free of damage.
Strength
Concrete masonry produces some of the most robust and durable materials for construction. CMUs are weather-resistant and capable of handling heavy loads. It also provides protection from break-ins and fires, which can lower insurance rates for further cost savings.
CMU Applications
CMUs can form the basis of many projects benefitting architects and end users. They come in many forms and styles to suit multiple applications, and you can tailor the finish to suit your project’s design.
Due to their many benefits, CMUs are preferred for foundation, basement, partition, interior and exterior walls. In addition, you can finish them with several coatings to prevent water penetration and complement the space’s appearance, including epoxy, urethanes and different paints.
CMU options suit many construction needs, from basic jobs to elaborate architecture. Some of the many finishes available include:
- Ground face finish: This type is on one side for a smooth finish and can be produced in a variety of colors for any application.
- Split face finish: This finish features added depth and dimension for aesthetic appeal.
- Antique finish: These are finished with a shot blast to display the stone beneath for a rustic, weathered look.
- Recycled: Take sustainability a step further and start your project with recycled CMU available in many finishes.
- Polished block: This innovative product gives the block a highly polished finish achieved through an expertly executed grinding process. Polished block is an excellent choice to give something unique to a project and bring out the aggregate’s natural beauty.
- Monarch traditional: The length and depth of a regular CMU combine with the height of standard brick to create a clay brick look.
CMU Block Shapes
Blocks may be solid or hollow with two or more cores. This feature reduces the cross-sectional area of the block by about one quarter. The advantage with this material is that its lighter weight makes it easier to work with. It can also be reinforced with rebar, either horizontally or vertically, depending on your plans.
Hollow concrete blocks are also a more economical choice, since they require less raw material, time and energy to produce. Once delivered, they are much easier to lift into place than their solid counterparts.
The fully solid blocks have different applications including caping off top of a wall or to give a building additional security. Since they are more expensive than their hollow counterparts, the cost of using them would always need to be weighed when considering whether they are the best solution for any project.
It’s important to use the right type of block for the job at hand. Examples of different types of block available and their uses are as follows:
- Stretcher Unit is a block that is laid flat on its bed and installed along the length of a wall. Its face is parallel to the face of the wall.
- Quion Corner Unit — pronounced “coin” — is the decorative end piece of a concrete block wall. These units are hollow and may be slightly larger than the surrounding block to give off a stronger appearance. These units are also called, “universal corners”
- Stretcher With Score Unit is a concrete block that is meant to be seen end on. The score unit gives it the look of brick.
- Solid Quion Corner Unit is similar to the Quion Corner Unit above — the only exception is that the block itself is solid.
- “L” Corner Unit is meant to finish an outside corner and be viewed from three sides.
- Closed Bottom Bond Beam Unit is hollow with parts of the end and crosswebs formed to allow a continuous channel to allow reinforcing steel beams and grout.
- Open Bottom Bond Beam Unit is a similar product to the Closed Bottom Bond Beam Unit, with the exception that the bottom is open. It can still accommodate steel beams and grout.
- Bullnose Stretcher Unit has one of its edges rounded off.
- Split 6 Flute Stretcher Unit is a six-inch concrete block with a decorative fluted or scalloped edge on the outside.
- Split 6 Flute “L” Corner Unit is from the same collection. It’s a corner unit featuring the same fluted edge for an outside corner.
- Split 8 Flute Stretcher Unit is an eight-inch concrete stretcher unit with a decorative scalloped pattern.
- Split 8 Flute “L” Corner Unit matches the eight-inch concrete stretcher for outside corners with the scalloped pattern.
- Split Wide Stretcher Unit features a decorative pattern with four sections per concrete block.
- Split Wide Corner Unit is the coordinating piece for outside corners. It features three pattern sections on one side and two on the other for pattern continuity.
Concrete Blocks: A Sustainable Building Product
The majority of the materials used to make CMU can be found in most places. Cement is an ingredient that is usually produced on a regional basis as well. It is the one building material that is produced close to a job site.
- The concrete industry uses waste products such as fly ash from combustion and blast furnace slag from iron manufacturing to produce concrete. Using them means 15 million metric tons of industrial waste is diverted from landfills annually.
- Using these materials reduces the CO? level in concrete by up to 70 percent. Typical reduction levels are in the 15-40 percent range.
- Concrete is recyclable. When it has served its original purpose, it can be crushed and used as aggregate, base material for roads, concrete slabs, or sidewalks. The crushed material can also be used as fill. The reinforced steel in concrete can also be made with recycled materials.
Recycled CMU
Recycled CMU is the eco-smart option for your project. These CMUs are made with 30 percent recycled material and are available with Nitterhouse Masonry Products’ Ground face and Split face finishes.
You have the option of ordering your CMUs with a higher percentage of recyclable material, if desired. Recycled materials can also be added to any color CMU block at the time of ordering. Using recycled CMUs benefits you in the following areas:
- Locally Sourced Materials: Points are given when materials are used from within a 500-mile radius. All the recycled CMUs from Nitterhouse Masonry Products are regionally sourced.
- Recycled Materials: Using recycled materials and resources to manufacture products also qualifies for LEED points. Nitterhouse Masonry Products uses a large percentage of recycled aggregates in their CMUs, and since the recycled materials are post-consumer, the products qualify for the maximum number of LEED points.
- Construction Waste Management: Since CMUs are modular in design, they produce very little waste during installation. Nitterhouse Masonry Products encourages its customers to return any unused product. These examples of construction waste management strategies qualify a project for another LEED point.
- Energy and Atmosphere: Walls constructed from masonry are a good choice for the interior of a structure, since they change temperature slowly and store coolness that can be emitted back into the building during business hours. Using concrete block on the interior walls of a building is a good strategy to absorb moisture, which will create a more comfortable interior atmosphere for the building’s occupants. Up to two LEED points may be earned in this category.
- Innovation and Design: Projects can earn LEED credits for projects that exceed the requirements of LEED Ratings. Credits have been awarded previously for impact-resistant finishes, durability, mold resistance and finishes that do not need painting. A total of four points are available in this category. Nitterhouse Masonry Products offers permanent colors that do not need painting.
Trust Nitterhouse Masonry for Superior Quality Concrete Masonry Units
Any time you undertake a construction, landscaping or design project, you stake your professional reputation on the outcome. Nitterhouse Masonry can help you stand out with our selection of quality masonry products for commercial and residential applications. We pride ourselves on our customer service and will go the extra mile to ensure you have what you need on time according to your budget.
Whether you seek inspiration for your next project or need a reliable provider you can trust, Nitterhouse Masonry is here to help you. Browse our product selection or contact us today for more information.
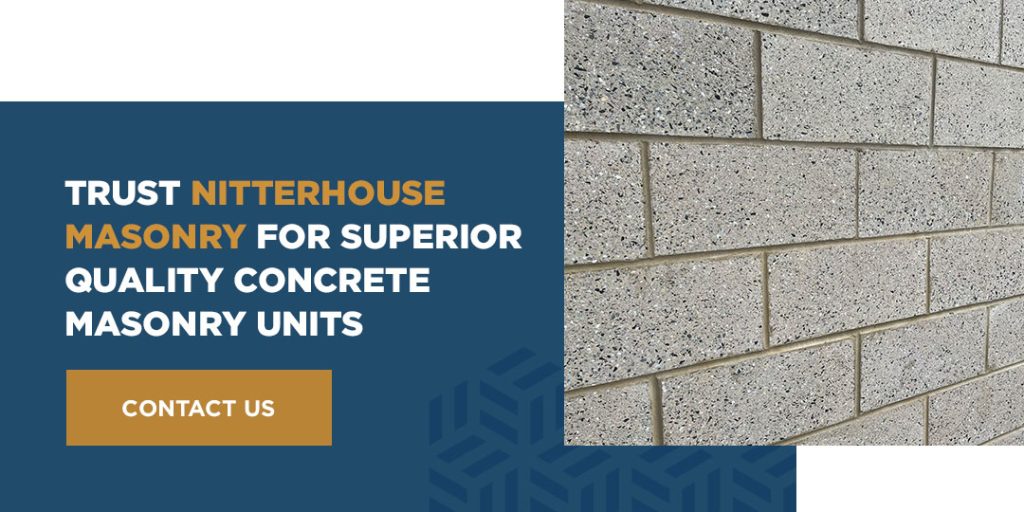